October 1, 2018
Two big tips for snow and ice efficiency
BY MARK BRADLEY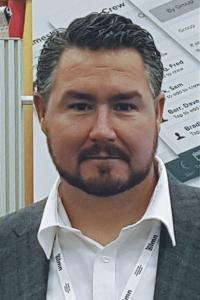
Reduce salt usage and expense
Early warnings are saying the winter of 2018/19 might be really challenging for snow contractors, when it comes to salt. Frequent late events last year, combined with work stoppages at mines, are prompting vendors to issue early warnings about potential salt shortages, especially in the Ontario area. Early salt pricing is higher than normal, and alternative arrangements are almost twice the price of ‘normal’ salt.Unless you like skyrocketing expenses and angry customers, you may have no choice but to carefully manage your salt this year. So here are some good tips:
Plan (and estimate) your salt usage for each site. Don’t just guess a price. Have a clear plan for how much salt (per average event) you will need to use for appropriate deicing coverage. Then measure your site; use online measuring tools without even leaving your desk!
Multiply the size of your site by your salt application rate to get the pounds of salt you need. (For example: 1.5 acres times 500 lbs./ acre = 750 lbs. for a 1.5-acre site).
Measure your salters to establish pounds per minute. To measure your salt application rate, first buy a decent scale (it’s worth it!). Get your spinner/auger going, then use a bag to catch salt for 15 seconds. Weigh the bag. Now multiply the weight by four — that’s how many pounds of salt come off the salter in one minute.
This is a good start. Now you should have a good idea how many pounds or tons of salt you need. You can give this to your drivers to help them apply the right amount of salt in an average event. But do you know how hard it is — at 2:45 a.m. in the middle of a blizzard — to weigh how much salt has come off your truck?
A better way to measure your salting is by using time (in min- utes) instead of pounds. Anyone who can drive a truck, can keep a loose eye on a clock.
Calculate how many minutes it will take (on average) to apply the correct quantity of salt. Divide the pounds of salt required for your site by the pounds-per-minute dispersed by your spinner/ auger. (Example: 750 lbs. divided by 115 lbs./min. = 6.5 minutes).
Share your anticipated salt use (per site) with your crews. If you are using paperwork, issue pages with average salting times per site. (But you really need to move to an app!). If you have gone paperless with an app, feed the app with that information, so crews are prompted with expected salt times as soon as they clock in.
Build site maps that train better plowers
If you are not building site maps for all your sites, you are really missing out. Maps don’t take much time, and all you need is Internet access. We have always gone to Google Maps, taken an overhead shot of the property, then highlighted the following areas so anyone dispatched to a site can see exactly what needs to be done.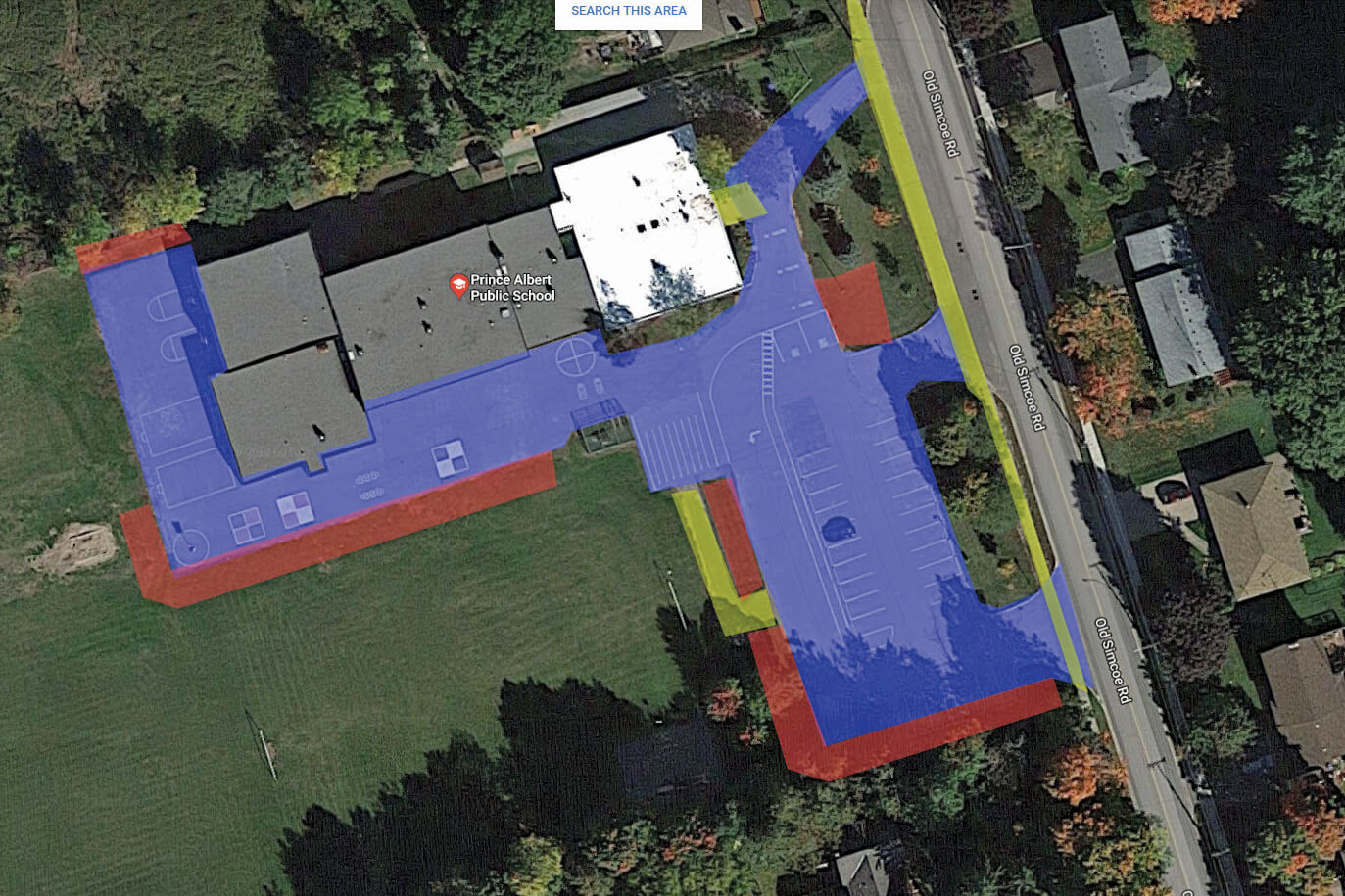
As an example:
- Blue areas for plowing
- Red areas are approved areas for piling
- Yellow areas are sidewalks we must clear
We spent about four minutes, start to finish, on the map above.
But now we have a system that:
- Helps ensure work gets done right, the first time.
- Makes it easy to send other drivers (without making mistakes).
- Can be signed or authorized by our customer before the first event, to ensure the scope of work is clear and accurately understood by all parties.
That site map is a good start, but it can be even better. We found a further decrease in mistakes and callbacks when we:
- Asked the customer about past issues or problems with snow and ice.
- Added notes and instructions directly on the site map.
- Added the estimated average plow and salt times to the site.
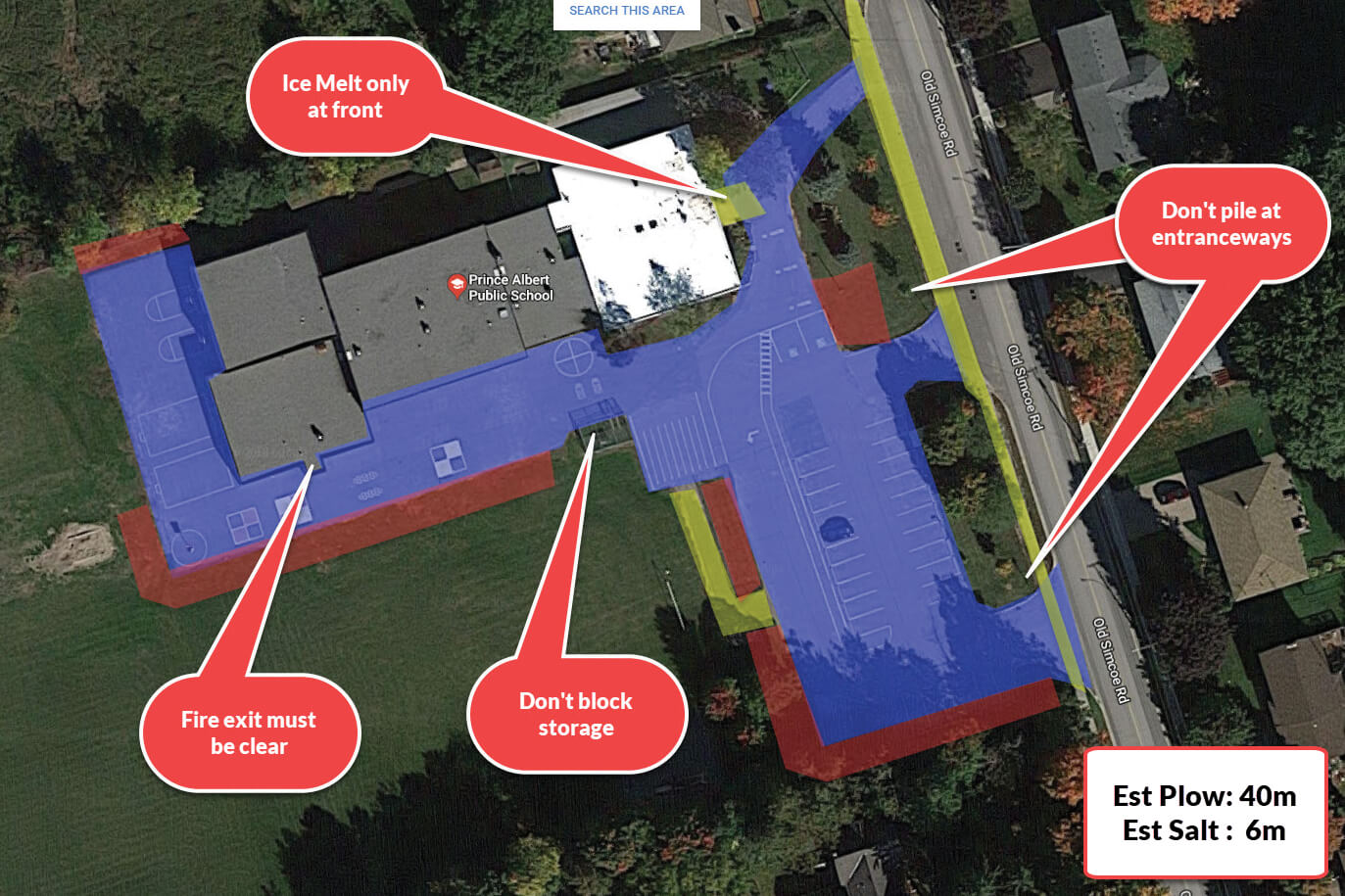
Now the site map serves as a complete visual reference for the team, to make sure they don’t miss any non-obvious issues.
Now we have a map that prevents mistakes and helps ensure the job is done correctly without any callbacks or customer frustration. But we can still make it better.

If you are paying attention, you have likely noticed your best plowers are 20 to 50 per cent faster than your less-experienced plowers. They have the same equipment and tools, but they know how to attack the site more efficiently. They start in the right places, push to the right places, and minimize backing up and turn-arounds.
So now that you have your maps, sit with your best plowers, and in less than two minutes per site, you can discuss the best way to clear it. Add numbers (for order) and arrows (for direction), and print these maps. Even better, simply upload them to your snow and ice app, and you have a system that could teach your grandmother how to clear better than most contractors!
These two little systems have made a big impact on our winter profitability. Less salt, fewer mistakes, and fewer callbacks help take care of my biggest expenses in snow and ice. They will do the same for you.
Mark Bradley is CEO of LMN and the former CEO of TBG Environmental, both based in Ontario.